Cosa fare e perché è meglio prevenire: la nostra proposta a un cliente, importante azienda farmaceutica multinazionale della provincia di Frosinone, per evitare il rischio di stop agli impianti.
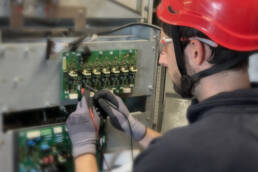
Le aziende farmaceutiche e alimentari operano in ambienti altamente regolamentati, in cui la conformità alle normative igienico-sanitarie è un parametro invariabile: le camere bianche sono un elemento fondamentale nella catena produttiva perché minimizzano la contaminazione microbiologica e particellare. Per mantenere queste condizioni, ma anche per evitare costose interruzioni della produzione, è essenziale la manutenzione programmata.
Le camere bianche dipendono da un’infrastruttura tecnologica avanzata: sistemi di filtrazione dell’aria, controllo della temperatura e dell’umidità e sistemi di alimentazione continua dell’energia elettrica. Un guasto improvviso, in particolare un’interruzione della fornitura elettrica, può compromettere istantaneamente le condizioni sterili richieste, rendendo inutilizzabile tutto il materiale in lavorazione.
Le conseguenze di un’interruzione elettrica nelle camere bianche possono essere disastrose: se i parametri di temperatura, pressione e filtrazione dell’aria non vengono mantenuti nei limiti previsti, la produzione in corso deve essere scartata per il mancato rispetto dei requisiti igienici. Questo comporta perdite economiche significative, spreco di materie prime e ritardi nelle forniture ai clienti.
Per prevenire queste situazioni la nostra proposta per un cliente, azienda multinazionale farmaceutica, si è articolata in varie fasi:
Abbiamo messo innanzitutto in atto tutte le operazioni previste dal Site Assesment Danfoss sugli inverter delle unità di trattamento aria di tutti i reparti. Si tratta di un servizio che prevede un’indagine completa in loco e un’analisi dei rischi dell’intera base installata di drive e che serve per registrare le condizioni delle risorse, la criticità e lo stato del ciclo di vita. Sulla base di questi parametri, ma anche della documentazione tecnica, viene calcolato un risultato di rischio per ogni drive.
Questa analisi completa viene riassunta in un report personalizzato e dettagliato, che diventa la base per un piano di manutenzione futura.
Le operazioni di manutenzione programmata vengono stabilite durante le fermate già previste degli impianti per manutenzione ordinaria.
Un’ulteriore analisi strumentale ha riguardato le ventole con più di 50mila ore di lavoro, quindi praticamente a fine vita e per questo a rischio di causare il fermo. Successivamente procediamo con un intervento annuale programmato, per attività di manutenzione ordinaria.
L’analisi ci ha fornito dati in base ai quali abbiamo anche proposto il retrofit di alcuni inverter ormai obsoleti e non più riparabili.
Tutto questo fa parte della nostra filosofia di intervento, non sui guasti, ma prima che i guasti avvengano: è il miglior servizio che possiamo rendere a clienti per cui il fermo impianti determina perdite spesso significative.
L’adozione di un piano di manutenzione programmata è una necessità per le aziende farmaceutiche e alimentari che operano in camere bianche, ma anche una buona pratica per qualunque altro tipo di linea produttiva: evitare guasti imprevisti significa continuità produttiva, efficienza e compliance con gli standard di ogni settore.
Contattaci ti richiameremo il prima possibile!
Condividi
Ti possono interessare anche:
Come un bullone allentato ha fatto riconsiderare la manutenzione a una grande azienda alimentare
L'importanza della manutenzione programmata degli impianti industriali
Il vantaggio di evitare lo stop alla produzione, la visione di una grande azienda
Manutenzione programmata per evitare lo stop e il ricorso all’assistenza
Le nostre intelligenze per impianti produttivi sempre più sicuri e efficienti
La gestione di un impianto implica molte attività. Per alcune è utile l’Intelligenza artificiale. Altre non possono…